From Typical to Digital: Recognizing the Evolution of Cloth Printing
The improvement of towel printing from typical techniques like block printing and resist coloring to contemporary strategies such as display and digital printing notes a significant change in the textile market. Traditional techniques, steeped in artisanal craftsmanship and cultural relevance, have progressively paved the way to electronic technologies that offer unmatched accuracy, effectiveness, and personalization. This transition not only improves production capabilities however likewise aligns with expanding demands for sustainable methods. Yet, how do these advancements impact the essence of cloth printing, and what might the future hold for this ever-evolving craft?
Traditional Towel Printing Techniques
In the early phases of fabric production, conventional cloth printing methods offered as the cornerstone of material layout, supplying both performance and artistic expression. Block printing, one of the earliest approaches, involved sculpting elaborate designs into wood blocks, which were then dipped in dye and pushed onto material.
Withstand dyeing, consisting of strategies like batik and tie-dye, utilized wax or other substances to protect against dye from penetrating particular locations of the material. This method created striking contrasts and intricate layouts, typically imbued with cultural value. Stenciling, another conventional method, involved reducing patterns right into a product and applying dye via the openings, providing a simpler yet effective method to create recurring styles.
These standard methods not just formed the fabric industry's early advancement but also prepared for future advancements. Each method reflected the cultural and regional qualities of its origin, protecting and disseminating artisanal understanding through generations.
The Rise of Screen Printing
The arrival of display printing in the early 20th century noted a substantial departure from conventional approaches, offering extraordinary adaptability and performance. Display printing made it possible for developers to produce elaborate patterns and vibrant colors on materials, which were formerly testing to accomplish with block printing or hand-painting techniques.
Among the key benefits of display printing is its capability to replicate complicated layouts widespread with amazing integrity. This scalability made it profoundly preferred in the industrial fabric sector, where mass manufacturing without sacrificing high quality is extremely important. Screen printing fits a vast array of inks and dyes, increasing the palette of textures and finishes available to developers.
In addition, the process is very versatile, appropriate for numerous fabric kinds consisting of cotton, silk, and synthetics. This flexibility, incorporated with its cost-efficiency for huge runs, strengthened display printing's duty as a keystone of modern textile manufacturing. Thus, the increase of display printing reinvented the industry, pushing the boundaries of what was possible in fabric style.
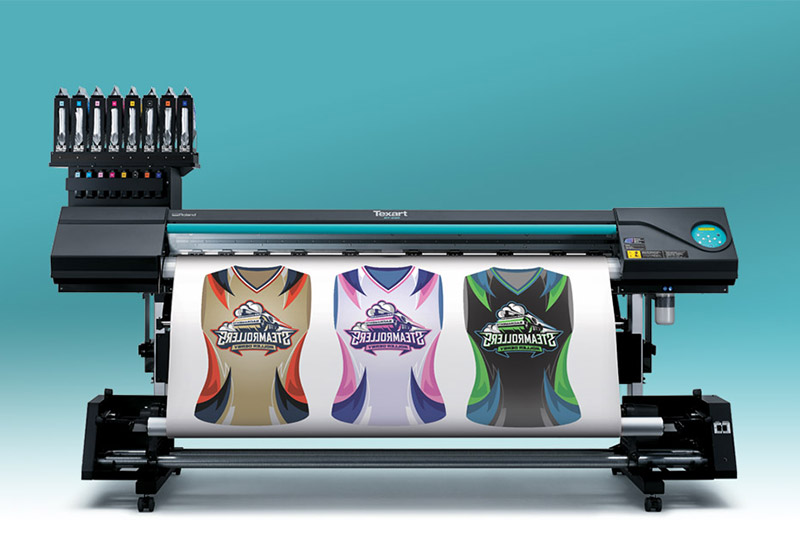
The Arrival of Digital Printing
Building on the amazing improvements brought by display printing, the textile industry experienced an additional groundbreaking development with the advent of digital printing. Emerging in the late 20th century, digital printing reinvented the way styles are transferred onto textiles, top article offering extraordinary versatility and efficiency. Unlike conventional approaches, which commonly required substantial arrangement and considerable hand-operated treatment, digital printing uses computer-aided layout (CAD) technology to generate intricate patterns directly onto the textile with high precision.
This innovation has actually made it possible for textile makers to satisfy the expanding need for modification and on-demand manufacturing. By getting rid of the need for plates and displays, electronic printing lowers preparations and reduces product waste, making it a much more sustainable choice. The ability to print complex pictures and a variety of colors in a solitary pass has actually opened up brand-new creative avenues for designers, promoting a rise in creative expression within the sector.
In why not check here addition, electronic printing supports smaller sized batch production runs, which is particularly helpful for niche markets and startup fashion brand names. This technical leap has not just boosted operational efficiency yet likewise equalized accessibility to top quality textile printing, establishing the stage for future advancements in material style and production.
Contrasting Strategies: Standard Vs. Digital
While both electronic and typical printing methods have their own one-of-a-kind advantages, they differ significantly in terms of procedure, performance, and environmental effect. Traditional towel printing, encompassing strategies like block printing and display printing, includes hands-on labor and elaborate craftsmanship.
In contrast, electronic printing utilizes advanced modern technology to move designs straight onto fabric making use of inkjet printers. Digital printing is substantially faster, permitting for quick turn-arounds and just-in-time production, which reduces the demand for large inventory storage space.
From an environmental point of view, digital printing is normally more lasting. It uses much less water and generates very little waste contrasted to conventional approaches, which commonly involve substantial washing and dyeing procedures. As a result, electronic printing is progressively preferred in an era where ecological considerations are paramount.
Future Fads in Cloth Printing
One considerable pattern is the boosted application of electronic printing modern technologies. Digital fabric printing is anticipated to dominate the market, driven by its efficiency and adaptability to consumer demands for personalized and limited-edition products. screen printing.
Additionally, the unification of smart fabrics, which incorporate electronic elements into fabrics, is readied to change the market. These textiles can give added performances such as temperature regulation, health surveillance, and interactive attributes. As my explanation technology continues to advance, the crossway of digital printing and wise textiles will open up new methods for innovative and functional applications in cloth printing.
Conclusion
The development of towel printing from traditional methods to electronic innovations marks a significant makeover in the textile market. While standard methods highlight artisanal workmanship and cultural heritage, electronic printing offers exceptional precision, efficiency, and modification.
The improvement of towel printing from conventional approaches like block printing and withstand dyeing to contemporary strategies such as display and digital printing notes a considerable shift in the fabric industry. Screen printing allowed developers to generate detailed patterns and vibrant colors on materials, which were previously testing to achieve with block printing or hand-painting methods.
Building on the exceptional developments brought by screen printing, the textile sector experienced another groundbreaking growth with the introduction of digital printing. screen printing. Standard cloth printing, including strategies like block printing and display printing, entails manual labor and detailed craftsmanship. As technology continues to advance, the intersection of electronic printing and wise textiles will certainly open new methods for functional and innovative applications in towel printing